Common problems of customers
Q1 | Where can I get the product information and price information? |
A1 | Please send us an email, we will contact you as soon as we receive your email. email: admin@dlhshjx.cn |
Q2 | How long can we get samples in a general way ? |
A2 | It depends on your project, usually 10-20 days can deliver. |
Q3 | How to enjoy OEM service? |
A3 | Generally speaking, we refer to your drawings or original samples, offer some techniques, suggestions and quotations to you. We will produce for you after you agree. we produce the drawing with your approval |
Q4 | What's kinds of information you need for quote? |
A4 | The production drawings can be sent in CAD, DXF, STEP, IGES, x_t and other formats, supporting the use of CAD, Soildwork UG ProE and other softwares. |
Q5 | Will the price change? |
A5 | If the exchange rate and material fee have not changed, it will not be changed. If there is any change, it will be notified in advance. |
Q6 | How If you produced bad quality products after deliveried? |
A6 | First of all, if the delivery is in time, our company will try our best and make the machining parts as soon as possible. The production fee for bad re-production is free, and the freight is also the responsibility of our company. If the deadline is too late, please ask the customer for help, the customer will repair it in Japan. Our company will only bear the amount of the customer's Invoice indication, and we will not be responsible for the addtional Invoice indication, We will try our best to reduce the rate of defective products to zero, and our goal is to ship all good products. At the same time, we will investigate the content of this defective product, investigate the responsibility, all the employees must participate in the defective product meeting to avoid the similar problems. |
Q7 | If there is defect in processing? |
A7 | According to the company's QC management requirements, production will be stopped immediately, report to the produce manager and analyze the cause of the bad condition. Specify a correction plan or scrap the production plan and re-submit the material production application. If we judged that the delivery or quality cannot be finished at this time, the actual situation must be notified with the customer. Use all the China's resources to find ways to solve problems. |
Q8 | What about the impact of exchange rate fluctuations on costs and profit? |
A8 | We will deposit the foreign exchange in the bank without exchanging it,unless the rate exchange to recover or when it has a smaller impact. If the exchange rate fluctuates too much, for long term cooperative orders, we will negotiate with the customer. |
Q9 | How to arrange the working time of the workshop? |
A9 | Usually, the factory is divided into two shifts. The first shift is from 8:00 am to 5:00 pm, and the second shift is from 5:00 pm to 1:30 am. If the work is very urgent, we will work overtime or even arrange three shifts. |
Q10 | What is the turnover rate of employees? |
A10 | The most of company's employees come from surrounding cities, so they are relatively stable. Turnover rate is 3-5 per year. |
Q11 | What is the delibery time? |
A11 | Generally it is 20-25 working days. If there is an urgent situation, it can be put forward at the time of quotation, we will make a quotation according to the parts and the delivery period. In the case of an urgent delivery time, the price of the parts will increase. |
Q12 | How if the drawing tolerances can not guaranteed? |
A12 | We will confirm the tolerance we can reach with the customer before the quotation. If the customer agrees to the tolerance adjustment, then we will make a quotation. If the machining process cannot guarantee the tolerance due to the force majeure technology, we will contact with the customer to discuss the solution in time. |
Q13 | Where are you buy the materials? |
A13 | The general materials are available in the Chinese market. Dalian is the main distribution place for Japanese companies to invest in China. As early as 20 years ago, it has formed a good supporting capacity (including raw materials). General carbon steel (S25C, S35C) , S45C), iron (SS400), die steel (SKD11, SKD61, SKS, SCM, etc.), copper (C3604, phosphor bronze, pure copper, etc.), aluminum (5052, 5056, 6061, 6063, 6082, 7075 , 7071, 2017, 2014, etc.), stainless steel (304, 316, 303, and SUS440C, etc.), insulating materials (POM, PE, PP, PEC, PVC, nylon, etc.) These materials are available in the Dalian market. Special materials which are not produced in the Chinese market or materials specially requested by customers are basically purchased through overseas material distributors in Shanghai and other places. The general material procurement cycle is 3-7 days. Special 7-15 days. |
Q14 | What is the average age of a worker? |
A14 | The average age of a worker is 30, only 5 or 6 are interns from the school. |
Q15 | Is the factory personnel stable? Will there be frequent demission? |
A15 | In general, most of the personnel are relatively stable. There are individual interns or new hires may be out of sorts or can not do the job. Employees who have worked for more than three years are relatively stable. |
Q16 | The packaging is too thick, could you make the packing thinner when you deliver the goods? |
A16 | According to our years of experience, also for the customer's product can arrive safely, we think the current packing thickness is suitable. If the package is too thin, in the process of transportation, there is likely to be bump against. This will affect the delivery date of the customer. In addition, we use specially light air bubble film for packaging, the impact on package weight and shipping costs is also minimal. Before shipment, we should consider not only the problem of freight cost and the convenience of splitting after delivery, but also the security of product delivery.We have more than ten years' experience in transporting goods to and from Japan, please be assured that we have the ability to pack our products well. Of course, we are more willing to listen to your opinion, hoping to improve our delivery service capacity better. |
Q17 | What is the relationship between Dalian Hongsheng Machine Co., Ltd and Flortc? |
A17 | The name of factory is Dalian Hongsheng Machine Co., Ltd, and Flortc is the window of foreign business, mainly aimed at the Japanese market. |
Q18 | Is there any delay in delivery in your company? |
A18 | Our company will strictly arrange production according to the delivery date specified by the customer, generally, no tardiness will occur. However, due to the complexity of the production process and other reasons can lead to production errors, in the process of remanufacturing, the delivery date may be delayed. We apologize for this. Measures: Related workers work overtime, try to do it in the shortest possible time, minimize the damage. We will analyze the reasons for the long production cycle and consider the solutions comprehensively. |
Q19 | Do you have a way to get confidentiality for our drawings per the requirements in agreement? |
A19 | Yes, Initially, we will control the using of the drawings and documents customers provided strictly, won't disclose to any third party. If some workflows of the item have to be helped by our other long-term cooperated factories, we will let our customers know and attempt to get the approval from our customers in advance. Secondly, all the documents you provided are keeped by the sales representative secretly who you contact with. It doen't allow to leaf through drawings and document without the permission. Finally, The customers information is confidential, if there is the customers' information shown on the drawings, our sales representatives will cover them with a blank. we name a group of letters as the customers's name and write it on our production drawings. So Others including the machinists won't recoginize the information of customers. |
Q20 | Is there training for the new workers? |
A20 | Yes, there is There are not only the educational training for the new staffs, but a sort of strict management system of promotion examination. As for the one who has never worked on machining industry, we have 3-year plan to cultivate them to be a professional one. We assign posts according to their personal capability and status. New staffs have a test which divided into Mechanical common sense theory and Practical Application for every stage. The test score and the daily performance are the rational basis for their wage adjustment. the new-comers who have or have not the working experience has a senior for a comprehensive guidance, from the basic knowlege to the grasping of the practical technological knowlege, and can begin their formal work after their capability being accepted. In addition, In order to creat a learning environment like a school and prompt every new employee to be grow up in this field, there are trainings for comprehensive quality education, business etiquette, safety production, recognization on the drawings from foreigners, emergency interconnection, 8S management education(Seriri, Seiton,Seiso, Seikeetsu, Shitsuke, Safety, Save, Study). |
Q21 | What is The proportion of technical staffs to the processing staffs? How long have they working here? |
A21 | There are 15 technological staffs currently which is approximately 25% of the staffs currently who working in the workshop. We share exchanges of experience on the early morning every single day to have new comers improved and absorbed. |
Q22 | Does every equipment has the regular checking and maintainess? |
A22 | there are amount of funds being invested to introduce the world's most advanced equipments which maintained twice by original manufactures annually. We will settle down the issues in the bud due to we do a cautious work. for example, we will do check and maintainess work before operating and start if check result is well. |
Q23 | How do you manage so many kinds of materials? |
A23 | 1.There is no material in our warehouse.We purchase materials according to the part size after receiving the customer's order every time. |
- Tel
- *Title
- *Content
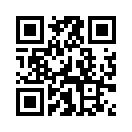
Subscribe to:
sign up for the latest catalogue, new design and promotion
- Tel:
86-411-87516616-828
- Email:
- hongsheng@dlhshjx.cn
- Address:
- 19-2, Liaoning Street, Jinpu New District, Dalian City, Liaoning Province, China.